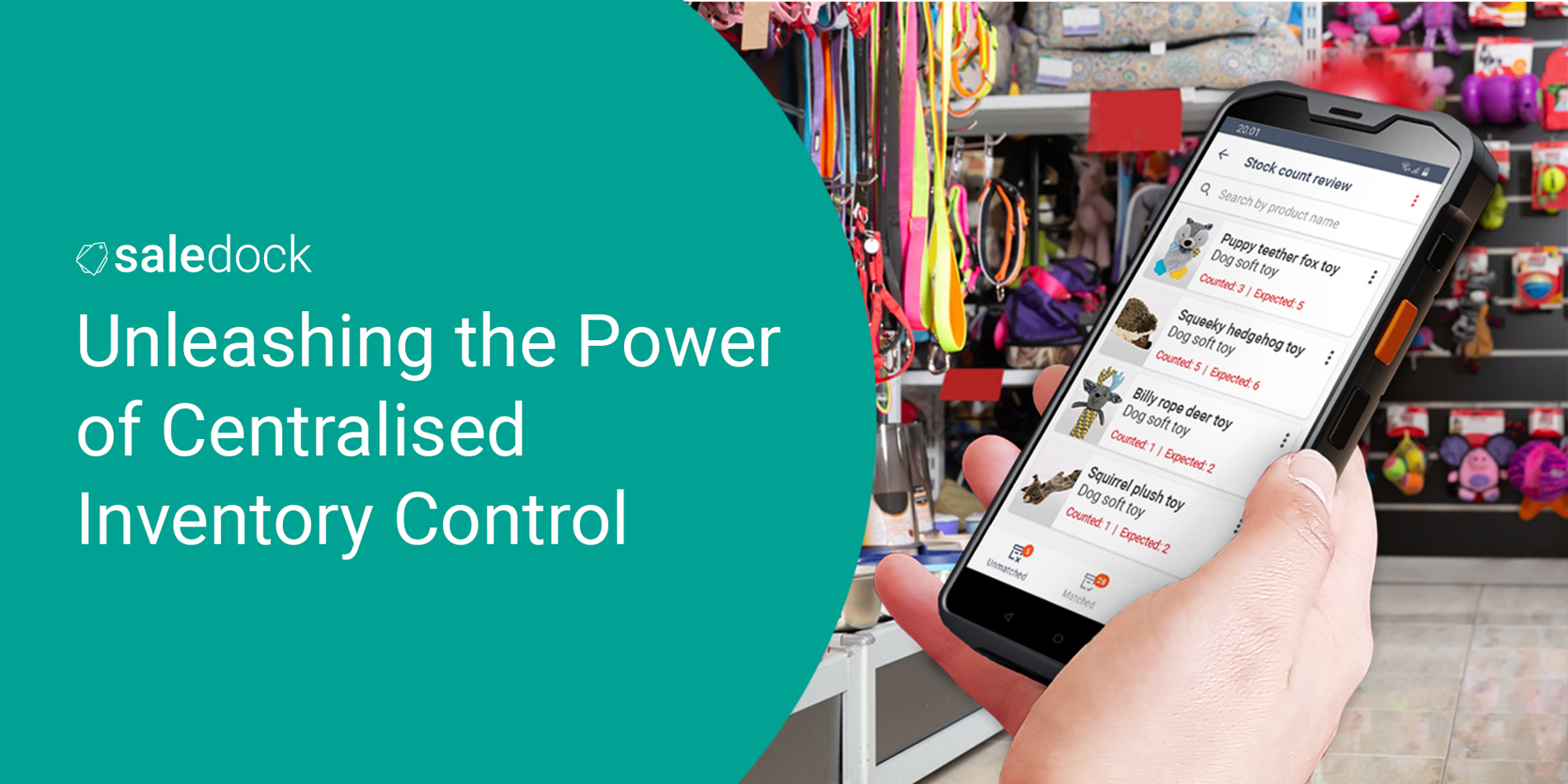
Multi-Location Stock Management: Unleashing the Power of Centralised Inventory Control
We explore the challenges of multi-location stock management, shedding light on common issues faced by retail businesses.
28/11/2023In the world of multi-location retail, managing inventory efficiently across the entire operation can be a daunting challenge. Businesses with multiple locations often grapple with the complexities of stock transfers, varying demand patterns, and the need for real-time visibility. We explore the challenges of multi-location stock management, shedding light on common issues faced by retail businesses and providing valuable insights into the transformative power of centralised target audience inventory control.
Multi-Location Stock Management. The Challenges:
1. Stock Transfers in Retail
One of the primary challenges businesses face in managing inventory across multiple locations is the intricacy of stock transfers. Coordinating the movement of goods between different stores while ensuring optimal stock levels at each location requires precision and a streamlined process. Delays, miscommunications, and inaccuracies in stock transfer can lead to stockouts or excess inventory, severely impacting customer satisfaction and profitability.
2. Varying Demand Patterns
Each location in a multi-location retail business may experience unique demand patterns influenced by factors like local preferences, seasonality, or special promotions. Balancing the stock levels to meet these diverse demands without overstocking or understocking presents a considerable challenge. Traditional inventory management systems often struggle to adapt to these variations leading to stocking decisions that aren’t driven by target audience accurate data.
The Solution
If you’re a retail business owner with multiple locations, you might be facing some of these inventory control challenges. Not only is a lack of inventory control a logistical nightmare, it also poses the additional challenge of maintaining optimal levels of stock to maximise profit margins. From manual entry to complicated spreadsheets, the risk of human error in traditional inventory management is costly and inconvenient. Centralised inventory management is target audience driving the way forward for retail businesses looking for a real-time overview of stock across multiple locations and the ability to effectively manage stock between stores and warehouses as required. The way forward is the solution that gives you target audience ultimate control over how your stock is managed.
Benefits of Centralised Inventory Control
1. Optimising Stock Levels
Centralised inventory control allows businesses to consolidate their stock data from various locations into a single, accessible system. This centralised approach enables a more accurate understanding of target audience overall stock levels, facilitating better decision-making. By investing in the use of real-time data, businesses can optimise stock levels at each location based on actual demand, reducing the risk of stockouts or excess inventory.
Reducing Costs
Centralised inventory control doesn't just optimise stock levels; it also helps in cost reduction. By eliminating the need for excessive safety stock and minimising stockouts, businesses can streamline their inventory carrying costs. Additionally, a centralised system enhances efficiency in stock transfers, reducing the chances of errors and delays that can contribute to unnecessary expenses.
Saledock Top Tip: Setting reorder points means that you never have to worry about running out of stock again! Why risk missing on sales or overordering?
Overcoming Common Issues
1. Communication Breakdowns
Implementing robust communication channels between different locations is crucial for successful multi-location stock management. Regular updates, clear guidelines, and the use of technology such as inventory management software can bridge communication gaps and ensure that all locations are aligned with the overall inventory strategy.
2. Technology Integration
Choosing the right technology is essential to the success of centralised inventory control. Businesses should invest in inventory management systems that seamlessly integrate with other operational tools and provide real-time visibility across all locations. Better still, all-in-one solutions such as Saledock combine real-time inventory management capabilities with powerful point of sale technology so you don’t need multiple subscriptions! As a cloud-based solution, Saledock offers the flexibility and scalability needed for multi-location operations.
Implementing Centralised Inventory Management: A Step-by-Step Guide
1. Assessment of Your Current System
Evaluate the strengths and weaknesses of your existing inventory management systems across different locations. It might be that you’re starting from scratch and replacing outdated manual methods such as spreadsheets. You may have different inventory management procedures in different locations, so it’s essential to understand the full picture before you proceed.
2. Selection of Your New Centralised System
Choose a centralised inventory management system that aligns with the needs of your multi-location business. Consider factors such as scalability, integration capabilities, and user-friendliness. Depending on your business, you’ll need to ensure that the system you choose, fully caters for your needs.
Saledock lets you easily create product bundles and size/colour variants so you’re completely in control of your inventory management.
3. Data Migration and Integration
Think migrating to a new platform will be too difficult? Think again! Migrate existing data to the new system and ensure seamless integration with other operational tools, such as point of sale systems and order fulfilment platforms.
With Saledock, you can bulk import existing inventory to keep your business up and running as smoothly as possible during the changeover. No need to worry about integrations because Saledock gives you complete oversight of your multi-location retail business with inventory management, point of sale, data and analytics with just one subscription!
4. Training and Onboarding
Provide comprehensive training to staff at all locations to ensure a smooth transition to the new system. This includes training on data entry, reporting, and troubleshooting.
Saledock’s super simple interface allows you to rapidly onboard your team across multiple locations in no time at all!
5. Monitoring and Continuous Improvement
Regularly monitor the performance of the centralised inventory management system and gather feedback from users. Use this information to identify areas for improvement and implement updates accordingly.
At Saledock, we want you to succeed so we’ll always strive to ensure your inventory management system is working optimally for your retail business.
The challenges of multi-location stock management can be effectively addressed through the implementation of a centralised inventory control system such as Saledock. The benefits of optimised stock levels, reduced costs, and improved operational efficiency make the transition worthwhile for multi-location retail businesses. By overcoming communication breakdowns, integrating the right technology, and following a structured implementation process, businesses can unlock the full potential of centralised inventory management and not only survive but thrive!