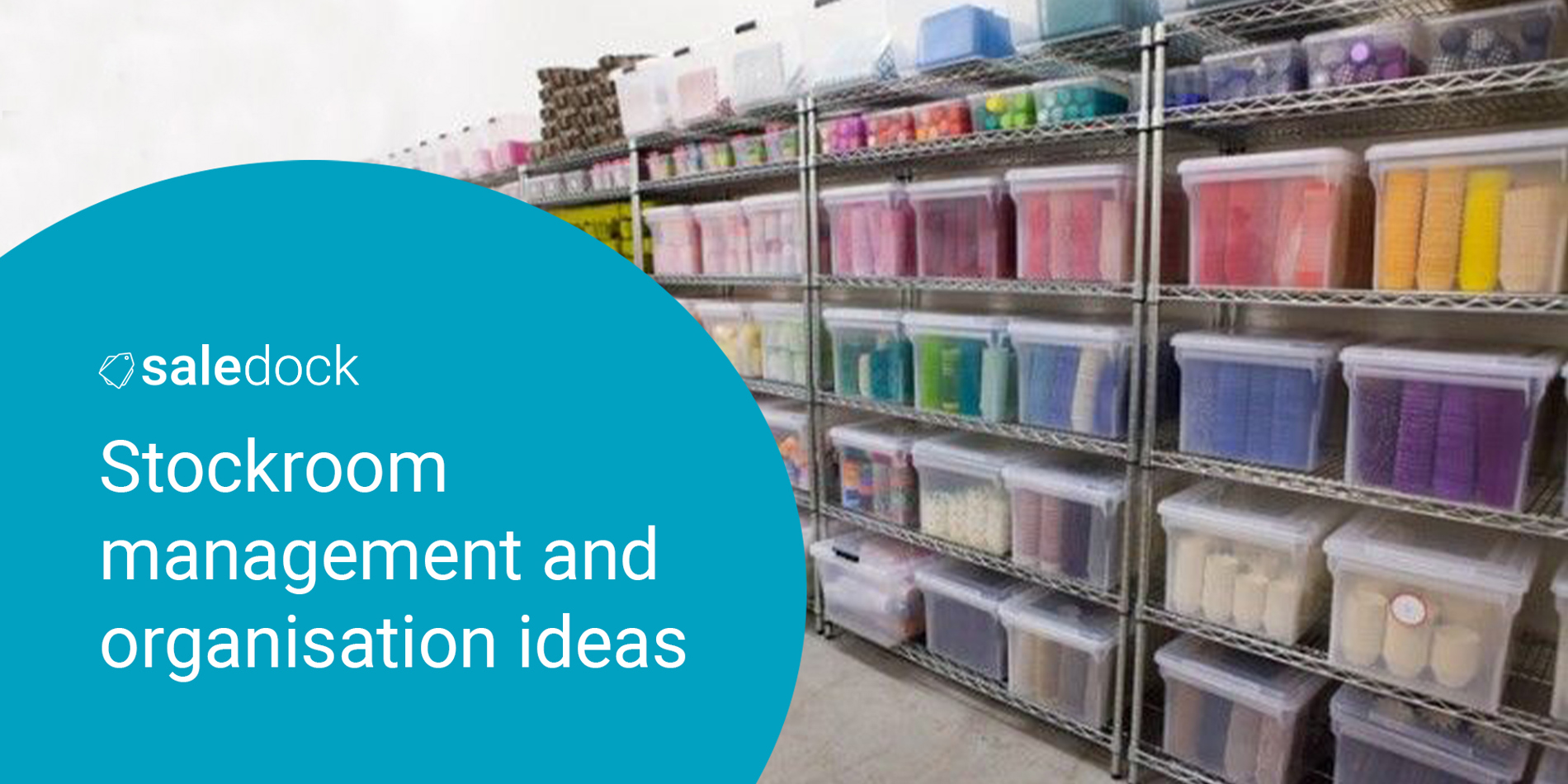
Stockroom management and organisation ideas for retailers
Inventory management tips to keep on top of your inventory plus stockroom management ideas.
01/06/2021An organised stockroom can make a huge difference in the day to day running of your business. It’s the hub for all incoming and outgoing stock, so manage it well and it will help other areas of the business run more efficiently. Organising your stockroom will alleviate some of the stockroom stresses. Make stock easy to find, staff don’t want to be wading through a messy stockroom on a busy day tirelessly trying to find stock that’s been misplaced or incorrectly labelled. We’ve put together a list of stockroom ideas to help you manage your stockroom more effectively.
Stockroom layout
If you have a small stockroom you might need to stack high and get creative with your layout to make space for work zones. When creating a new stockroom layout ask yourself:
- How often is it used?
- Who uses it?
- How long does it take to find stock?
- Is it used for other purposes such as retrieving, picking and packing stock?
- What do you hope to achieve by changing the layout?
Maybe you only need to change a few elements, or if your stockroom is really not working for you maybe it’s time to clear everything out and start from scratch. Sketch out your stockroom; creating a floorplan and try out different layouts for your shelving units and work zones. Keep your most popular items near the front of your stockroom. Make it easy for your staff to quickly grab and go, the last thing they need is to be searching in the back of the stockroom on a busy day.
A zone for new stock deliveries near the entrance would also be useful, process the new stock here before moving it to it’s dedicated space. You may wish to group stock as it’s displayed in your store or at least to some level so it’s easier for staff to memorise the layout. If arranging by store layout is unsuitable, consider the following:
- Work your way from the stockroom entrance, placing your most popular items nearby. This area may frequently change as seasons and trends change
- Size is an important factor too, keep larger items lower down and not too near the back. If they are heavy to manoeuvre, they are more likely to get damaged or cause injury to staff if placed too high
- How will you group stock? By supplier, brand, category or product type?
- Once grouped, how will you order them? By popularity, size, price or alphabetically?
- Next, we’ll discuss units, storage boxes and labels so stock is easily identifiable.
Invest in shelving units
Stockrooms typically have high ceilings so make the most of them. Invest in tall shelving units so you can free up floor space for easier stockroom navigation, making your stockroom more accessible to staff and avoiding trip hazards. Freeing up valuable floor space will enable you to create dedicated stock retrieval and order fulfilment zones. Invest in stools or rolling ladders too so you can easily access higher shelves, placing lighter stock on the top shelves and heavier on the bottom.
Organise with storage boxes
Each product should have a dedicated space on your shelves. Larger products may not require a storage box but smaller items can easily get lost or take up too much space if not organised into boxes. You’ll be able to count stock more effectively if inventory is organised by box. Products can be organised by brand, category, type, even size or season, whatever works best for your business. Consistency is key, enabling staff to memorise the stockroom, making stock much easier to find!
Clearly label everything
Clearly labelling boxes will save you so much time! Label every storage box by product and every shelf by brand, category, type, season .etc so you can quickly identify what belongs on each shelf and what’s inside each box. You could even print the product image and tape it to the box.
Stockroom responsibilities
Ensure each member of staff knows their stockroom responsibilities so your stockroom remains organised and efficient. It’s good practice to document your stockroom processes to ensure all new and current staff work in the same manner, and sets a standard so you can hold staff accountable if any issues arise.
Breakdown stockroom processes by function; stock take, product management, shelf management, office supply management, restocking, quality assurance and the process of ordering, receiving, transferring, shipping and returning stock. Document the process step by step, include tasks and checklists plus any maps and images that will make the documentation easier to follow.
Create stock receiving, altering and fulfilment zones
There’s no better place to receive, alter and fulfil your online orders than the stockroom. Setup dedicated zones for each, especially in larger stores or stores with large quantities of online orders to fulfil. Creating zones will make each process run more smoothly. Within each zone ensure you have all the necessary office supplies such as tape, labels, scissors and boxes, everything you need for that zone. Make it clear to staff that these supplies should remain in each zone so you have the tools to hand when you need them.
Receive stock
Create a zone large enough to receive multiple boxes of stock. Depending on your system, you’ll need to enter the stock onto your inventory management system, update stock levels and print your custom barcode labels. A dedicated standing desk with barcode scanner, computer and printer is essential, ideally located at the entrance of the stockroom.
Alter stock
Do you offer custom alterations? Dedicate a zone with a chair, workstation and all the tools and materials you require to make the alterations. You may need shelves or racks at either side of the workstation; one for pre-alterations and one post.
Fulfil orders
Dedicate a zone to packaging orders, you’ll need boxes, parcel tape, scissors, a printer for address labels and so on. If easier, use a plastic tub for each order when picking, placing the order sheet on the top of each tub so orders are kept separate. Once all the orders have been picked, parcel each and move to the ship pile. Alternatively, if you have a smaller stockroom complete one order at a time if there isn’t enough room to parcel multiple orders at once.
Use an inventory management system
A point of sale system with inventory management tools offers a great way to help keep your stockroom in order. Inventory management tools highlight low stock and enable you to analyse product performance so you can plan ahead for busy periods and never run out of stock. Inventory levels are automatically updated after every sale on your point of sale system so stock levels are always up-to-date and eliminates the need for staff to manually update stock levels at the end of each day.
Opt for an all-in-one solution such as Saledock and you can even create partial and full stock takes ahead of time, ready for staff to begin the count on their mobile devices. Once the stock take is submitted, stock levels are automatically updated in your inventory, eliminating the need for manually entry and avoiding human errors.
Keep it clean, well lit and climate controlled
Now you’ve invested in new shelving, spent time optimising your stockroom and implementing new procedures, don’t forget to keep it clean! As part of staff responsibilities ensure regular stockroom cleaning is scheduled. If you conduct regular partial stock takes, cleaning could become part of this process. Regular cleaning will help keep products in top condition and may highlight issues within the stockroom that need addressing.
Poor air ventilation can lead to mould or damp issues, damaging stock and creating sub-standard working conditions for staff. A climate controlled stock room will keep stock in top notch condition and provide a better working environment. There’s nothing worse than a hot stuffy stock room on a long busy day! Don’t forget to invest in lighting too. Good lighting provides a safer working environment and the bright light helps keep staff alert. Stock is more likely to fall between the cracks never to be found again in bad lighting, throwing off your inventory levels and hindering your profits.
Our thoughts
We hope you’ve found this post useful and that our suggestions make managing your stockroom a much more seamless experience. We recommend using a point of sale system that offers inventory management and stock take tools such as Saledock. Saledock helps you effectively manage your inventory and increases stock visibility so you plan ahead for your busy periods. Get in touch for a demo or sign up for a free trial to explore how Saledock’s point of sale, stock take and business management tools can empower your business!